数控高频淬火机床凭借 “PLC 程序可定制 + 线圈快速适配” 的核心特性,突破了传统专用淬火设备 “一工件一设备” 的局限,能在同一台机床上完成齿轮、轴类、内孔件等多种工件的表面 / 内孔淬火热处理,完美适配多品种、小批量的柔性生产需求,其通用性的实现逻辑与应用价值如下:
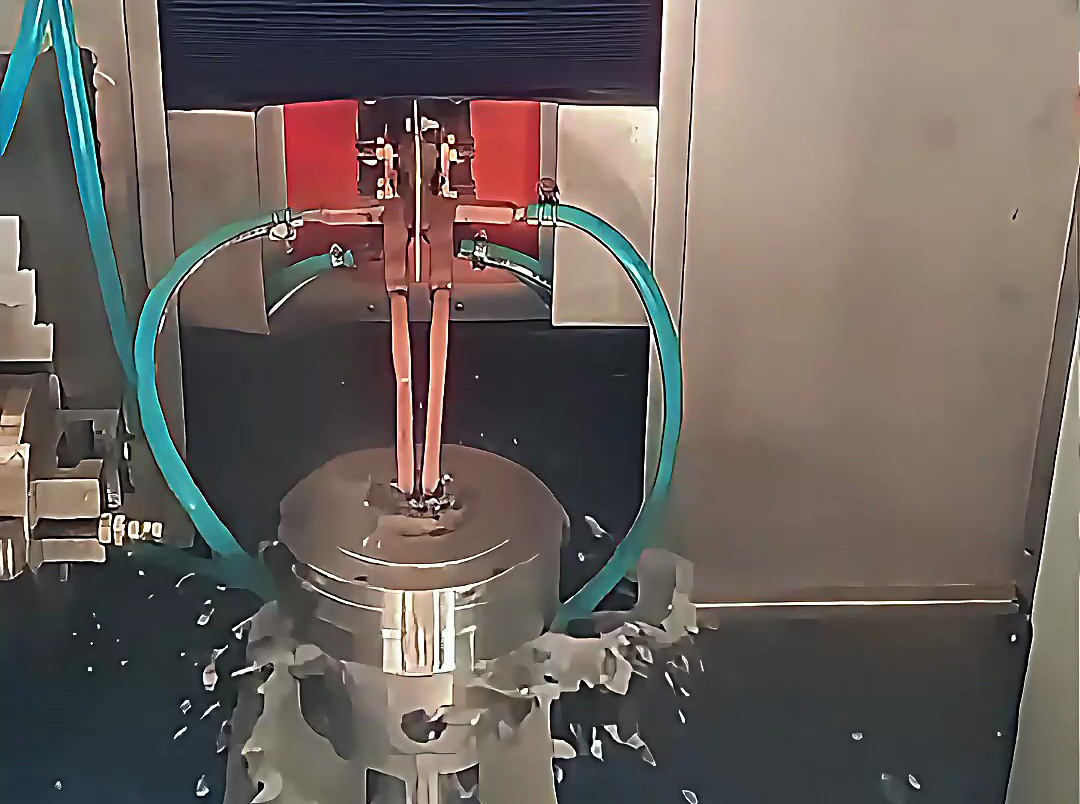
数控高频淬火机床的通用能力,源于 “软件可编程” 与 “硬件可更换” 的协同设计:
机床内置的 PLC 控制系统(可存储 1000 + 套工艺参数),通过修改程序实现对不同工件的精准控制:
加热参数:针对齿轮(模数 2-10)、轴类(直径 20-100mm)、内孔件(孔径 15-80mm),自动调整高频功率(5-50kW)、加热时间(2-20 秒)、旋转速度(5-30r/min)等关键参数(如齿轮需仿形加热 + 慢速旋转,轴类需环形加热 + 匀速旋转);
运动轨迹:数控轴(X/Y/Z 轴)按工件形状预设移动路径(如齿轮齿面淬火时,线圈随齿形轨迹进给;内孔淬火时,线圈沿孔深方向匀速移动),确保加热区域与工件受力区精准匹配;
冷却协同:根据工件材质(中碳钢、合金钢)自动调节冷却水压(0.2-0.5MPa)和时间,避免过冷导致的裂纹或冷却不足导致的软点。
不同工件的几何特性(曲面、圆柱、内孔)需匹配专用感应线圈,机床通过快速换型设计(线圈更换时间≤5 分钟)实现通用:
齿轮专用线圈:仿齿形 “梳状” 或 “环形” 线圈,与齿轮齿面保持 0.5-1mm 间隙,配合工件旋转(3-5r/min),实现齿面、齿根的均匀加热(硬度偏差≤±1HRC);
轴类专用线圈:环形线圈(直径比轴大 5-10mm),沿轴长方向平移加热(速度 0.5-2mm/s),确保轴颈、台阶面等关键区域硬化层深度一致(1-2mm);
内孔专用线圈:“棒状” 或 “伞形” 线圈(直径比内孔小 2-3mm),伸入孔内后通过径向扩张贴合孔壁,实现内孔表面硬化(如轴承孔、油缸内孔,硬化层深度 0.8-1.5mm);
通用基础线圈:针对异形件(如凸轮、偏心轴),可快速更换 “U 型”“L 型” 等简易线圈,配合数控轴的多维运动,完成非规则表面的淬火。
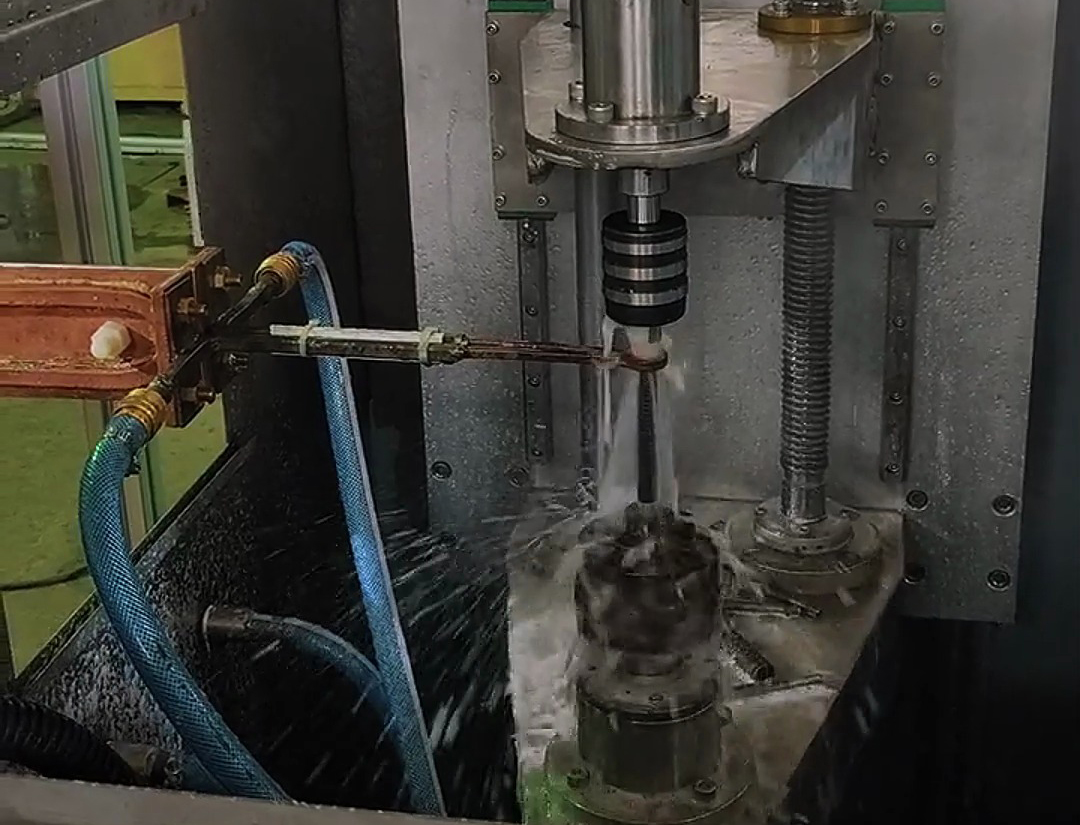
数控高频淬火机床对不同工件的处理,通过 “程序调用 + 线圈更换” 即可快速切换,典型场景如下:
工艺需求:齿面硬度 HRC55-60,齿根硬化层≥0.8mm,避免齿顶过热;
程序与线圈:调用 “齿轮淬火程序”,自动设定加热功率(15-25kW)、旋转速度(4r/min)、冷却时间(3 秒);搭配仿齿形线圈,线圈随齿轮齿廓同步运动(轨迹误差≤0.02mm),确保每个齿的加热均匀;
效果:齿面硬度均匀性达 98%,齿根弯曲疲劳强度提升 40%,满足汽车变速箱齿轮的重载需求。
工艺需求:轴颈表面硬度 HRC50-55,硬化层深度 1.2-1.5mm,轴身无变形(直线度误差≤0.03mm/m);
程序与线圈:调用 “轴类淬火程序”,设定轴向进给速度(1mm/s)、功率渐变曲线(从轴端到中部功率线性调整);搭配环形线圈,线圈与轴颈同心度≤0.05mm,确保圆周方向加热一致;
效果:轴颈磨损率降低 50%,在高速旋转(3000r/min)工况下无异常振动。
工艺需求:孔径 50mm 的油缸内孔,表面硬度 HRC58-62,硬化层深度 0.8-1mm,孔圆度误差≤0.02mm;
程序与线圈:调用 “内孔淬火程序”,设定线圈旋转速度(10r/min)、加热时间(8 秒);搭配内孔专用 “扩张式线圈”(加热时直径自动适配孔径),避免传统内孔线圈与孔壁间隙不均导致的加热偏差;
效果:内孔耐磨性提升 3 倍,液压系统泄漏率降低至 0.01%。
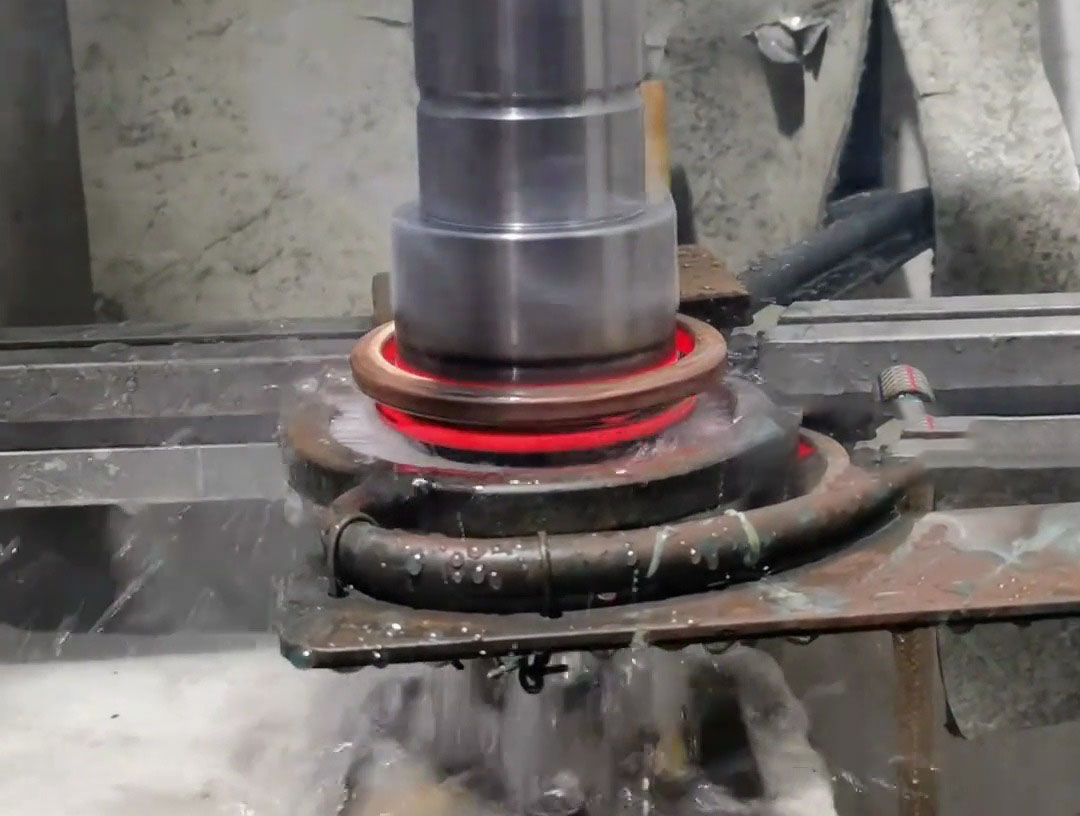
相比传统专用淬火设备(如齿轮专用淬火机、轴类专用淬火机),数控高频淬火机床的优势体现在:
对比项 | 数控高频淬火机床(通用型) | 传统专用淬火设备 |
---|
设备投入 | 1 台设备覆盖多工件,成本降低 60%-70% | 每种工件需 1 台设备,初期投入高 |
换型时间 | 程序调用 + 线圈更换≤15 分钟 | 需重新调试设备,换型需 2-4 小时 |
柔性生产 | 支持多品种、小批量(最小批量 10 件) | 仅适合单一品种、大批量生产 |
精度控制 | 数控定位精度 ±0.01mm,质量稳定性 99% | 人工调整,精度波动 ±0.1mm |
数控高频淬火机床在实现通用性的同时,通过以下设计确保淬火质量不打折:
数控定位系统:X/Y/Z 轴伺服电机控制精度达 0.001mm,确保线圈与工件的相对位置偏差≤0.02mm(避免局部过热或欠热);
闭环温控:红外测温仪实时反馈工件温度(采样频率 100 次 / 秒),PLC 自动调节功率(响应时间≤0.1 秒),温度偏差≤±3℃;
防变形设计:针对大尺寸工件(如长轴),程序内置 “分段加热 + 对称冷却” 逻辑,减少热应力导致的变形(变形量比传统工艺降低 50%)。
数控高频淬火机床的价值,在于打破了热处理设备 “专用化” 的桎梏,通过 “PLC 程序可编程 + 线圈快速适配” 的柔性设计,让一台设备具备处理齿轮、轴类、内孔件等多工件的能力。这不仅降低了企业的设备投入成本,更适应了现代制造业 “多品种、小批量、快换型” 的生产节奏,成为连接 “个性化需求” 与 “高效生产” 的关键热处理设备。