齿轮生产中,合格率与一致性的差距往往源于淬火热处理工艺的选择。许多高合格率厂家的 “秘密”,正是用高频淬火设备替代传统火焰煤炭炉 —— 这不仅是技术升级,更是对齿轮性能稳定性的根本保障,其差距体现在加热精度、工艺可控性与质量稳定性的全方位碾压。
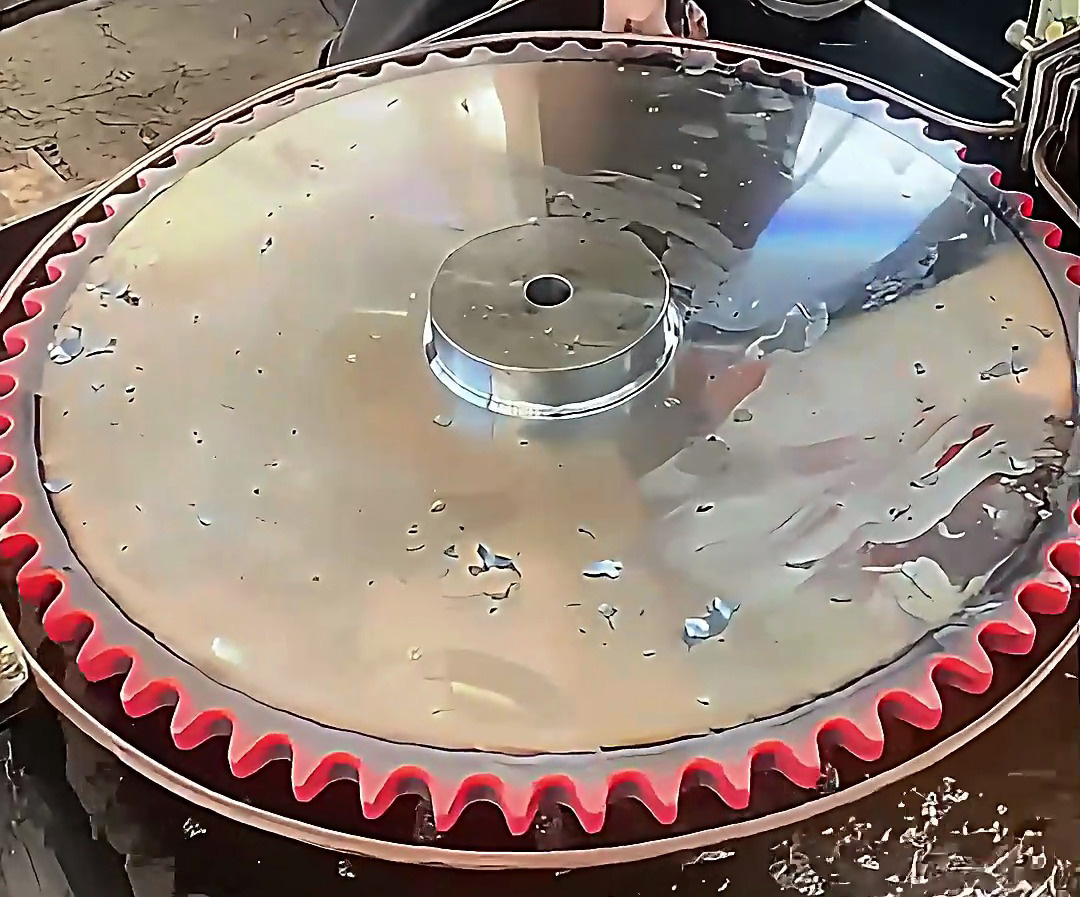
火焰煤炭炉(以焦炭、煤为燃料)通过明火直接加热齿轮,其原理决定了难以克服的短板,直接拉低合格率:
加热均匀性极差:煤炭燃烧的火焰温度分布混乱(中心区可达 1000℃,边缘区仅 600℃),齿轮不同部位受热不均,同一齿轮的齿面硬度差常达 ±8-10HRC(合格标准需≤±2HRC);
温度无法量化:依赖工人肉眼观察 “钢材颜色” 判断温度(如 “樱桃红” 对应 800℃),误差可达 ±100℃,导致部分齿过热(晶粒粗大、韧性骤降)或欠热(硬度不足、耐磨性差);
冷却时机滞后:从炉膛取出齿轮到喷水冷却的过程中,温度会自然下降 100-200℃,奥氏体化不充分,最终硬度达标率仅 70%-80%。
火焰煤炭炉燃烧时产生大量 CO₂、H₂O 和烟尘,齿轮在高温下会发生:
某小厂数据显示:火焰淬火的齿轮,因氧化脱碳导致的早期失效占比达 30%,而高频淬火可降至 1% 以下。
煤炭质量(热值波动)、炉温分布(每次添煤后温度骤升)、工人操作习惯(不同班次判断标准不同)等因素,导致同一批次齿轮的性能差异极大:
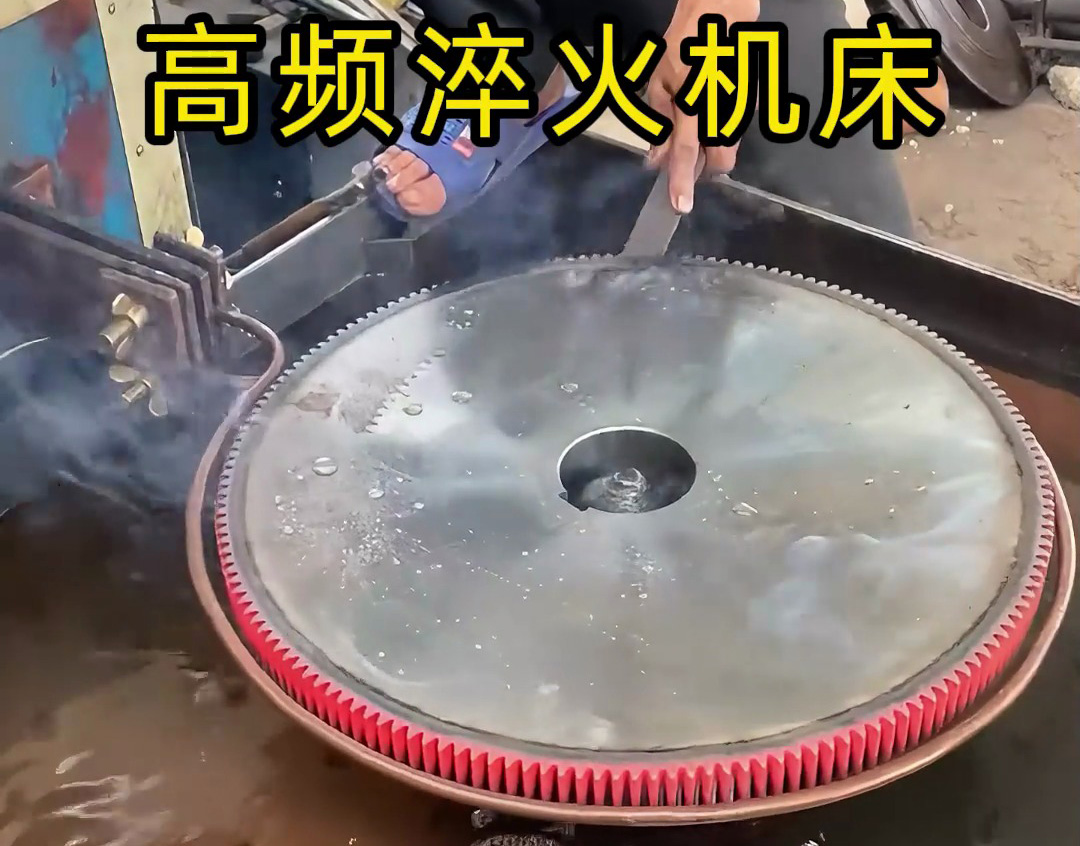
高频淬火(频率 30-100kHz)通过 “电磁感应加热 + 精准控温”,从根源上解决火焰炉的缺陷:
局部定向加热:定制化感应线圈贴合齿轮齿面,仅加热需淬火区域(齿面、齿根),非淬火区温度≤300℃,避免整体过热;
数字化控温:通过 PLC 程序设定加热温度(如 860±5℃),红外测温实时反馈,功率自动调节(响应时间≤0.1 秒),同一齿轮各齿温度差≤±5℃;
微秒级冷却控制:加热完成后 0.5 秒内自动启动喷雾冷却(压力恒定 0.3MPa),确保马氏体转变充分,硬度偏差可控制在 ±1HRC 内。
高频加热时齿轮不与明火接触,且可通入惰性气体(如氮气)保护,实现:
高频淬火的参数(功率、时间、冷却压力)可存储为程序,换班或换批次时直接调用,确保:
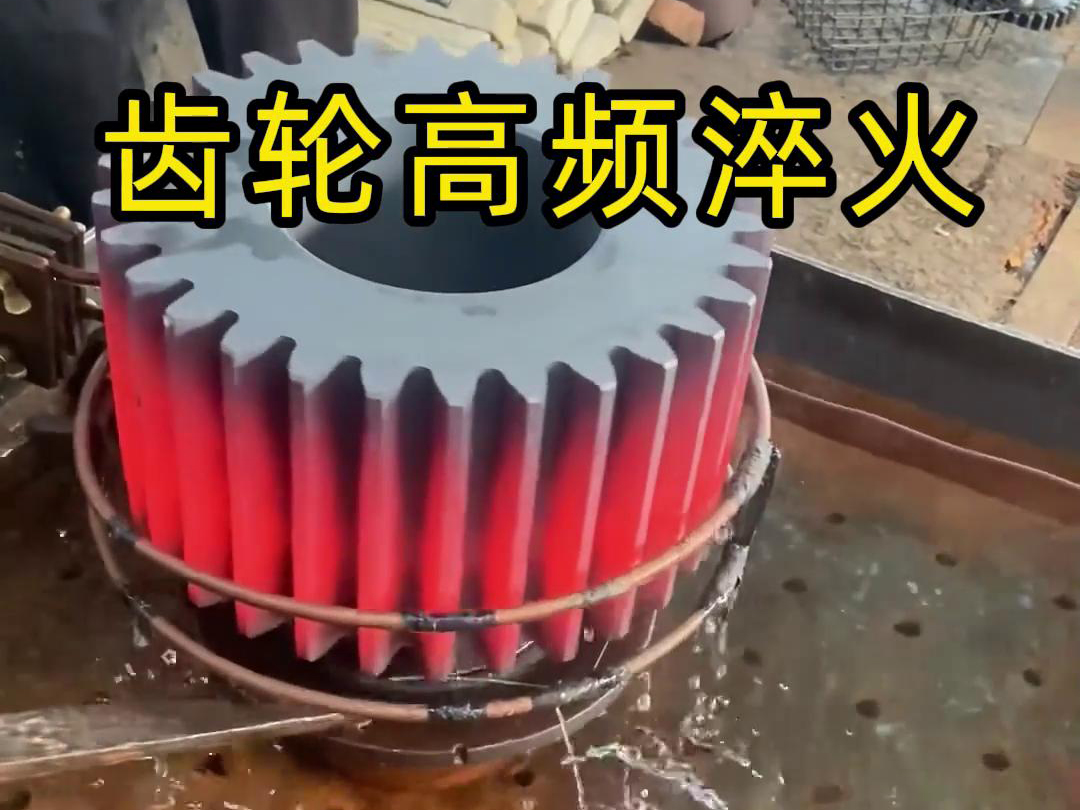
高频淬火设备的初期投入(10-30 万元)高于火焰炉(1-2 万元),但长期收益显著:
废品率降低:按年产 10 万件齿轮计算,高频淬火可减少 2 万件废品(每件成本 50 元),年节省 100 万元;
寿命延长:高频淬火齿轮的疲劳寿命是火焰淬火的 2-3 倍,客户退货率降低 90%,品牌口碑提升;
人工成本下降:1 人可操作 3 台高频设备,替代 5-6 名火焰炉工人(需添煤、看火、搬运),年省人工费 20-30 万元。
齿轮合格率与一致性的差距,本质是 “可控工艺” 与 “经验依赖” 的较量。高频淬火设备通过数字化、精准化的加热方式,将齿轮热处理从 “看天吃饭” 变为 “精准可控”—— 这就是优秀厂家不愿外传的 “秘密”。对于追求质量的齿轮厂而言,升级高频淬火不是 “选择”,而是 “生存必需”,毕竟在精密制造领域,“差不多” 的产品最终会被 “差很多” 的市场淘汰。