齿轮作为机械传动的核心部件,需同时具备表面高硬度(耐磨性)与芯部高韧性(抗冲击),淬火热处理是实现这一性能组合的关键工序。在火焰淬火、感应淬火、激光淬火等多种方式中,高频淬火设备凭借精准、高效、低变形的优势,成为齿轮淬火的主流选择,尤其适配多样化生产需求。
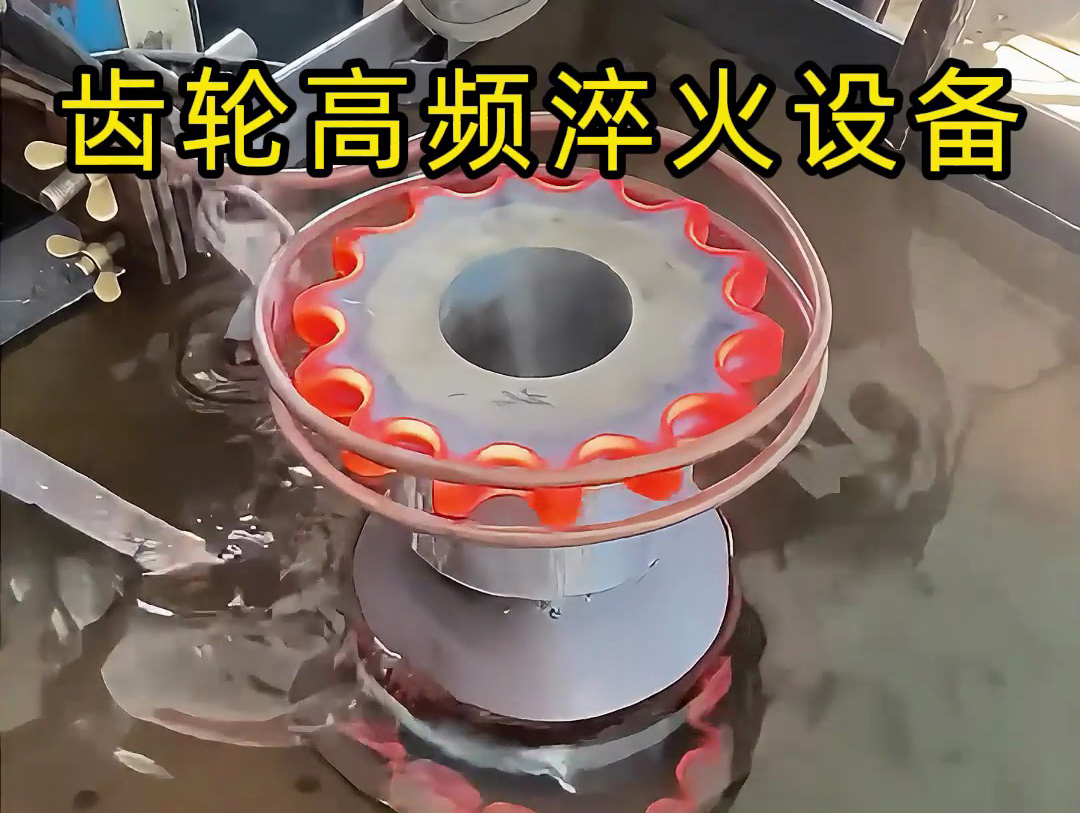
针对齿轮的齿面、齿根等关键部位,高频淬火(频率通常 30-100kHz)的优势显著:
淬火方法 | 加热精准度 | 效率(单件处理时间) | 变形控制 | 适用齿轮类型 |
---|
高频淬火 | 齿面温差≤±10℃ | 5-30 秒(根据模数) | 变形量≤0.05mm | 中小模数齿轮(m≤6)、精密齿轮 |
火焰淬火 | 齿面温差 ±50℃以上 | 1-3 分钟 | 变形量≥0.1mm | 大型齿轮、对精度要求低的齿轮 |
接触电阻淬火 | 局部易过热 | 20-60 秒 | 变形较大 | 简单齿形齿轮 |
激光淬火 | 温差≤±5℃ | 10-40 秒 | 变形极小 | 超精密齿轮(成本高) |
精准聚焦加热:通过仿形感应线圈(贴合齿形设计),将热量集中于齿面、齿根等易磨损区域,加热温度精确控制在 850-900℃(齿轮钢 Ac3 温度以上),齿芯温度≤300℃,避免整体性能受损;
高效批量处理:中小模数齿轮(如汽车变速箱齿轮)单件淬火仅需 10 秒,配合自动上下料系统,单小时产能可达 300-500 件,较火焰淬火提升 3-5 倍;
变形微乎其微:高频加热时间短(热影响区小),配合后续低温回火(180-200℃),齿轮公法线长度变动量≤0.03mm,齿向误差≤0.01mm/m,无需二次校直即可满足装配精度。

齿轮经高频淬火后,性能优化体现在多方面:
表面硬度:20CrMnTi 等渗碳齿轮钢齿面硬度可达 HRC58-62,较未淬火状态(HRC20-25)提升 2 倍以上,耐磨性显著增强;
抗疲劳性能:齿根处形成 100-200MPa 的残余压应力,抵消啮合时的交变拉应力,接触疲劳寿命延长至原来的 2-3 倍;
冲击韧性:芯部保持 HRC30-35 的韧性,在过载或冲击工况下(如汽车起步、换挡),齿轮不易断裂。
某汽车齿轮厂的测试数据显示,经高频淬火的变速箱齿轮,在 10 万公里路试后,齿面磨损量仅为传统淬火齿轮的 1/3,故障率降低至 0.5% 以下。
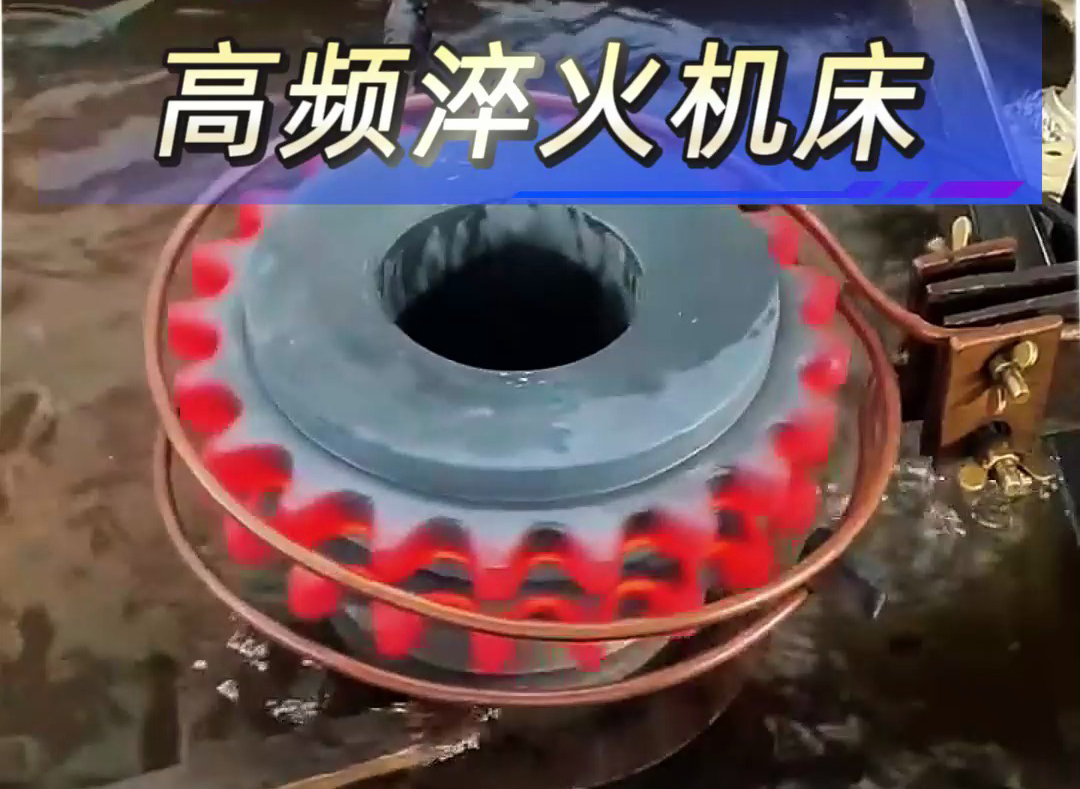
高频淬火设备的适配性广泛,尤其适合:
汽车、摩托车传动系统中的圆柱齿轮、锥齿轮;
机床变速箱内的精密齿轮(模数 1-6mm);
工程机械中的重载齿轮(需局部硬化)。
工艺实施中需注意:
线圈设计:根据齿形定制 “仿齿线圈”,确保每个齿面加热均匀(间隙 2-3mm);
冷却控制:采用喷雾冷却(压力 0.2-0.3MPa),保证齿面马氏体转变充分,硬化层深度控制在 0.8-2mm(模数越大,硬化层越深);
设备维护:每周清理线圈内的氧化皮,每月校准加热功率与时间的匹配性(确保同批次齿轮性能一致)。
高频淬火设备通过对齿轮关键区域的精准硬化,在保证效率与精度的同时,实现了 “耐磨齿面 + 韧性齿芯” 的性能平衡,成为齿轮制造中兼顾质量与成本的优选方案,直接影响齿轮传动系统的可靠性与使用寿命。若需针对特定齿轮类型(如异形齿、大模数齿轮)定制淬火方案,可随时咨询工艺细节。