对于厚度仅 0.8mm 甚至 0.1mm 的超薄工件,焊接过程的温度与时间控制直接决定焊接质量与工件完整性。超高频焊接机凭借 “微区加热、瞬时响应” 的特性,成为超薄工件焊接的理想选择,既能实现完美熔合,又能避免工件因过热而损伤。
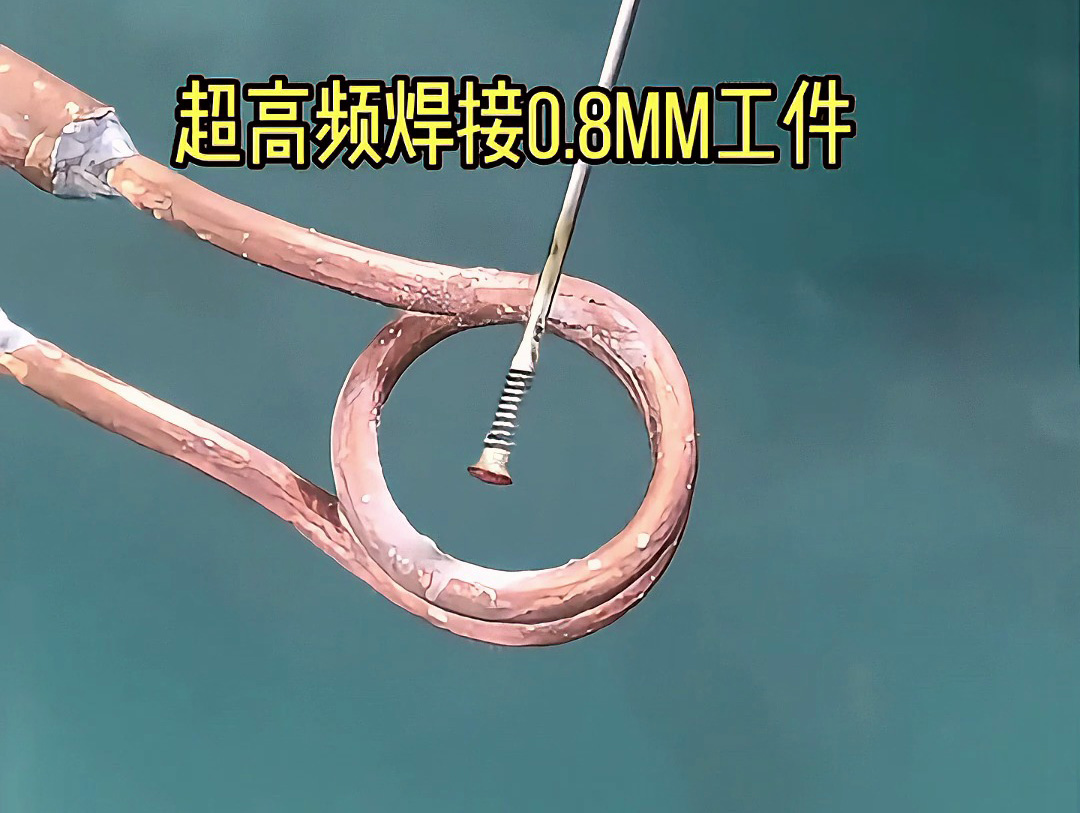
针对 0.8mm 厚度的工件(如精密电子元件的铜片、不锈钢薄片),超高频焊接机(频率通常 200-400kHz)的精细控制能力凸显:
温度精准可控:通过高频交变磁场(趋肤效应极强),将热量严格限制在焊接接口处,加热温度可精确控制在焊料熔点 ±5℃范围内(如焊接 0.8mm 铜片采用锡铅焊料时,温度稳定在 183-190℃),避免工件因温度过高导致的变形或性能退化;
时间微秒级调节:完成 0.8mm 工件的焊接仅需 0.5-2 秒,超短加热时间减少热传导对非焊接区域的影响,工件整体温升≤30℃,尤其适合对热敏感的电子元件或精密结构件;
焊缝均匀美观:超高频的能量聚焦使焊料熔融充分且分布均匀,焊缝宽度可控制在 0.3-0.5mm,无传统焊接的 “溢料”“虚焊” 问题,力学性能检测显示,0.8mm 不锈钢薄片焊接后的抗拉强度可达母材的 85% 以上。
某精密仪器厂的应用案例显示,采用超高频焊接机处理 0.8mm 铜质接线端子后,焊接合格率从传统高频焊接的 82% 提升至 99.5%,且因过热导致的端子氧化率几乎为零。
超高频焊接机的技术优势在 0.1mm 工件(如箔片、微型传感器电极)焊接中更具颠覆性:
微区能量聚焦:采用定制化微型感应线圈(直径可小至 0.5mm),将磁场能量集中于直径≤1mm 的焊接点,实现 “点对点” 加热,0.1mm 铝箔焊接时,非焊接区域温度仅上升 10-15℃,完全避免材料脆化;
动态响应速度:设备功率调节响应时间≤10 微秒,可根据焊料熔融状态实时调整能量输出,防止 0.1mm 工件因瞬间过热而烧穿(传统焊接机因响应慢,0.1mm 工件烧穿率高达 30%,超高频焊接可降至 0.5% 以下);
工艺适配性广:无论是金属箔片的搭接、异种材料(铜 - 镍、铝 - 铜)的微连接,还是微型元件的密封焊接,超高频设备都能通过参数微调(如 0.1mm 镍箔焊接采用 150kHz 频率、0.3 秒加热时间)实现稳定连接。
这类超精细焊接技术广泛应用于高精密领域:
医疗器械中的微型导管焊接;
航空航天的箔式传感器连接;
电子芯片的引线键合预处理。
操作时需注意:
线圈与工件的间距需精确控制在 0.1-0.2mm,确保能量聚焦;
采用惰性气体保护(如氩气),防止 0.1-0.8mm 工件焊接时产生氧化;
定期校准设备的功率与时间参数(每月 1 次),保证微米级焊接的一致性。
超高频焊接机通过对温度与时间的极致控制,突破了超薄工件焊接的技术瓶颈,既满足了 0.8mm 工件的精细焊接需求,又实现了 0.1mm 工件的稳定连接,为高精密制造领域提供了可靠的超微焊接解决方案。若您有超薄工件的焊接需求,可根据材料、结构定制专属焊接参数,欢迎咨询技术细节。