在棒料锻造生产中,全自动棒料锻造加热炉通过流程化设计,将送料、加热、成型环节无缝衔接,为批量生产提供了稳定高效的热加工方案。

这套设备的核心逻辑在于 “自动化流转”。送料机作为起始环节,可根据预设的棒料长度(支持直径 10-80mm 的圆钢、方钢)自动上料,通过输送辊道将棒料精准推送至中频加热炉入口。中频加热炉(频率通常 2-10kHz)利用电磁感应原理对棒料整体加热,根据材质特性调节参数 —— 例如 45# 钢棒料需加热至 1100-1150℃,加热时间随直径变化,直径 50mm 的棒料约需 40 秒,确保芯部与表面温度均匀(温差≤50℃)。
加热完成的棒料由机械夹具快速移送至冲床工位,夹具的定位精度控制在 ±0.5mm 以内,保证冲压时的位置准确性。整个过程无需人工介入,避免了传统人工送料时的高温烫伤风险,也减少了因操作节奏不一致导致的质量波动。
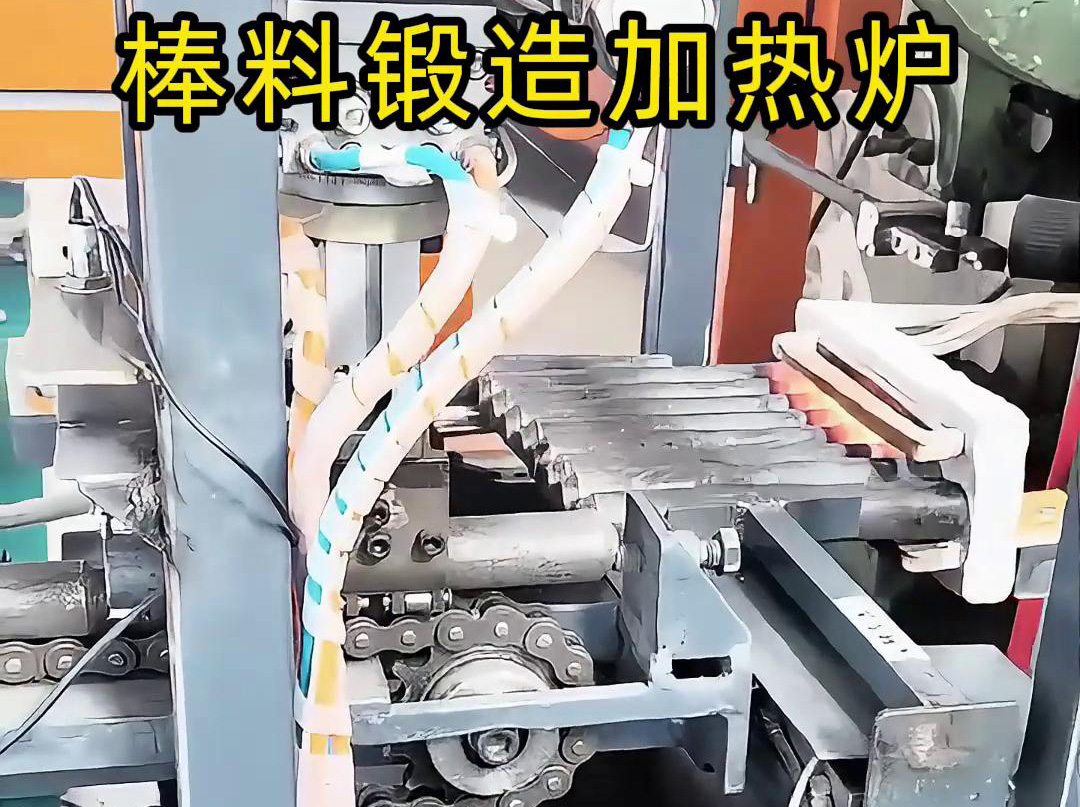
实际生产中,这套系统的效率优势显著。以直径 30mm 的棒料为例,传统人工线单班产能约 500 件,而全自动设备可达 1200 件以上,且冲压成型的尺寸一致性更好 —— 经检测,工件直径偏差从 ±0.3mm 缩小至 ±0.1mm,废品率降低至 1% 以下。
设备的适应性也较为灵活,更换棒料规格时,只需在控制系统中输入新参数(长度、直径、加热温度),调整送料机的截料尺寸和冲床的冲压力度,15 分钟内即可完成换型,满足多品种生产需求。
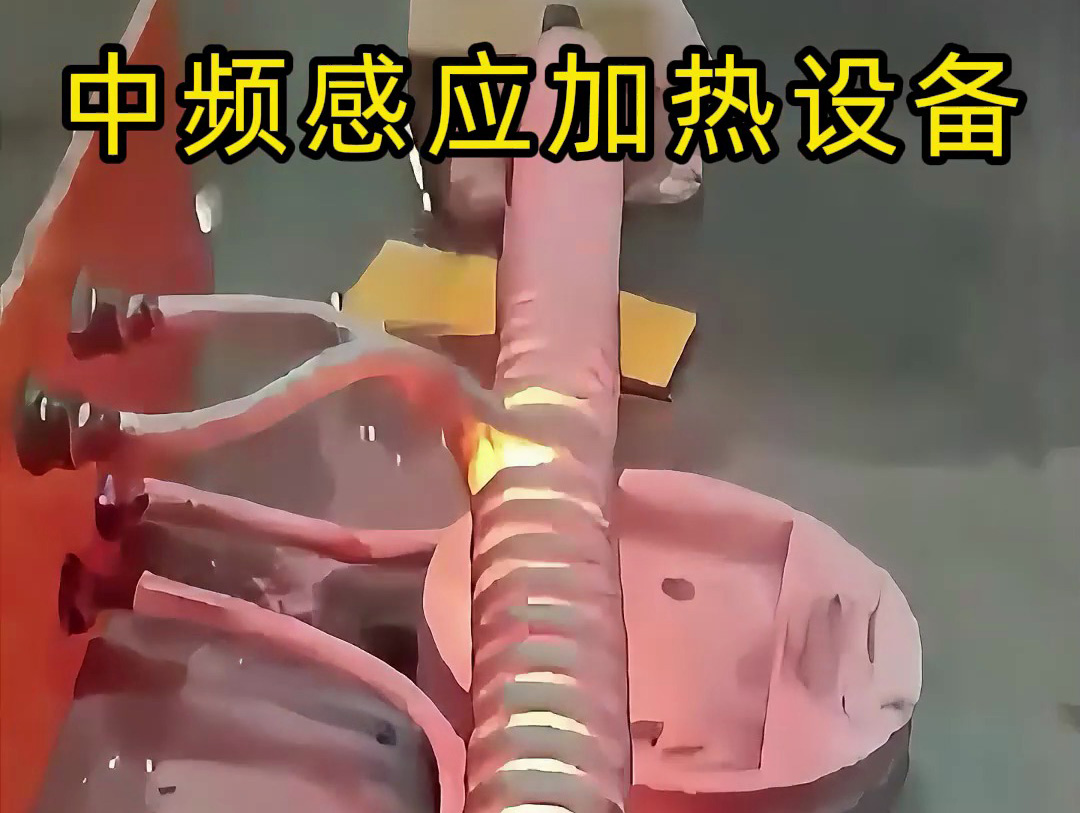
维护方面,需每日检查送料辊道的对齐度(防止棒料跑偏),每周清理中频炉内的氧化皮堆积,每月校准加热温度(用红外测温仪比对设定值与实际值)。按此规范操作,设备的连续运行稳定性可达 800 小时以上。
对于追求批量生产效率与质量稳定性的棒料锻造场景,这套全自动加热炉通过各环节的精准配合,既保证了棒料加热的均匀性,又通过自动化流转提升了整体产能,成为热加工领域的实用选择。