平面淬火热处理(如齿条齿面、导轨工作面、扁条受力面)通过高频淬火设备的在线化布局,实现 “工件连续通过线圈→自动加热→即时冷却” 的一体化流程,尤其适配长条形金属件的批量硬化处理,其核心优势在于效率、均匀性与自动化的完美结合。
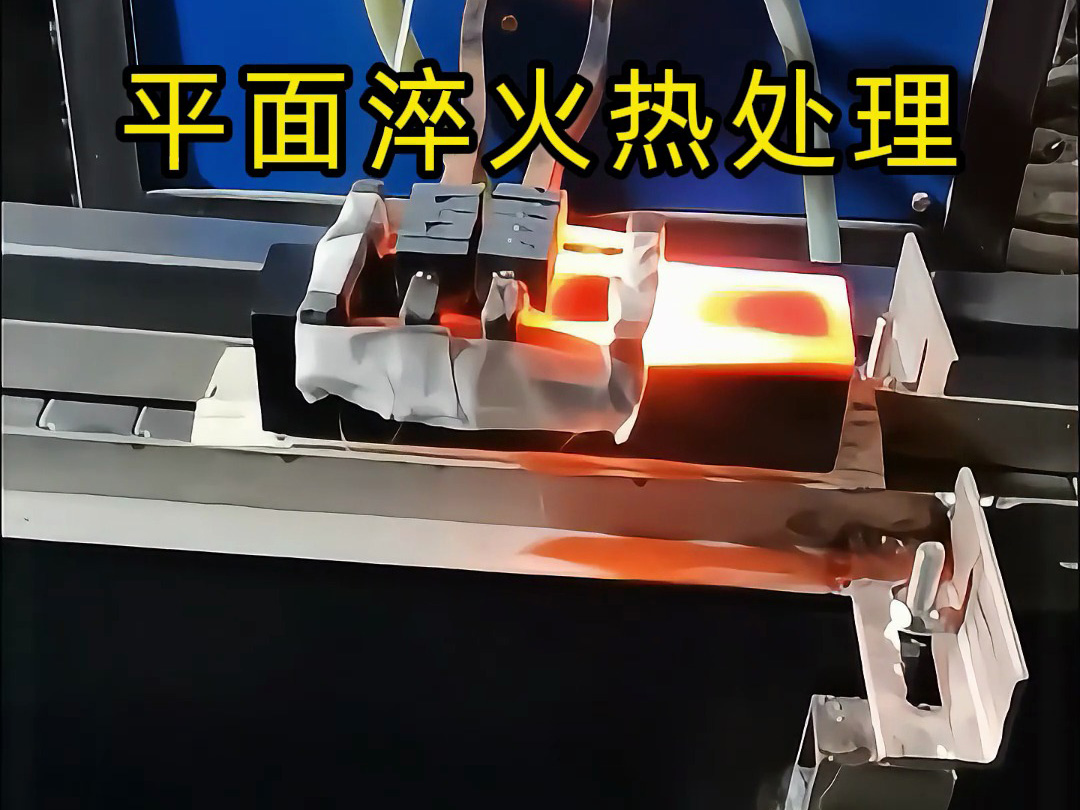
高频淬火设备在生产线中的固定安装,需围绕 “连续通过、均匀加热” 设计,典型布局包括:
线圈固定方式:采用扁平式感应线圈(宽度与工件平面匹配,如齿条淬火用宽度 50mm 线圈,导轨用 100mm 线圈),线圈与传送带保持 3-5mm 间距,确保工件平面与磁场均匀接触;
传送系统:由伺服电机驱动的辊道或链条传送带,速度可精准调节(0.5-5m/min),保证工件在 coil 内的加热时间恒定(通常 5-20 秒,根据硬化层深度需求设定);
冷却衔接:线圈出口处紧接冷却装置(喷雾或浸水),工件离开加热区后 0.3 秒内即可进入冷却,避免温度回落影响淬火效果。
以长 2 米的导轨平面淬火为例:设备功率 30kW,频率 30kHz,传送带速度 1m/min,工件通过线圈的加热时间为 12 秒,淬火温度达 860℃,冷却后表面硬度稳定在 HRC55-58,全程无需人工干预。
平面淬火对齿条、导轨、扁条等工件的针对性优化显著:
核心要求:齿面硬度 HRC50-55,硬化层深度 0.8-1.2mm,齿根过渡区需平滑(避免应力集中);
线圈设计:采用 “仿齿形扁平线圈”,仅加热齿面与齿根上部,齿底不淬火(保留韧性);
在线优势:10 米长齿条可连续通过,避免分段淬火导致的接头硬度偏差(传统离线淬火接头误差达 ±5HRC,在线淬火≤±1HRC)。
核心要求:导轨平面硬度均匀(偏差≤±2HRC),平面度误差≤0.1mm/m(避免滑动卡顿);
线圈设计:矩形宽幅线圈(覆盖导轨整个工作面),配合磁屏蔽装置(减少侧面加热);
在线优势:加热与冷却同步进行,热变形量仅为离线淬火的 1/3(某机床导轨在线淬火后变形量≤0.05mm/m)。
核心要求:扁条单侧边缘 2-5mm 宽度硬化(如农机刀片刃口),硬化层深度 0.5-1mm;
线圈设计:单侧开口的 “U 型线圈”,磁场集中于边缘区域,避免整体加热导致的变形;
在线优势:扁条通过速度可达 3m/min,单小时处理量超 100 米,较人工手持线圈淬火效率提升 8 倍。
为确保连续生产中的质量稳定,需满足三大技术条件:
功率动态调节:设备配备红外测温反馈系统,当工件厚度、材质存在微小差异时(如扁条厚度偏差 ±0.2mm),自动调整输出功率(±5% 范围内),保证加热温度恒定(误差≤±10℃);
线圈冷却系统:高频线圈工作时自身温度可达 150-200℃,需通过内置水冷管道(流量 2-5L/min)强制冷却,避免线圈过热导致的磁场分布不均;
防偏移定位:在传送带上设置导向轮(与工件侧边间隙≤0.5mm),防止工件通过时横向偏移(偏移量>1mm 会导致边缘漏淬),配合激光对中装置实时监测,偏移超限时自动停机报警。
对比项 | 在线高频平面淬火 | 离线人工淬火 |
---|
效率 | 连续生产,单班(8 小时)处理量超 500 米 | 单件装夹,8 小时处理量≤50 米 |
均匀性 | 同批次工件硬度偏差≤±1HRC,合格率≥99% | 偏差可达 ±5HRC,合格率约 85% |
热变形 | 连续加热 + 均匀冷却,变形量≤0.05mm/m | 局部骤热导致变形量≥0.2mm/m,需校直 |
人工成本 | 1 人监控整条线,无需频繁操作 | 2-3 人轮换装夹、加热、冷却 |
平面淬火热处理的在线化应用,是高频淬火技术与生产线自动化的深度融合,尤其适合齿条、导轨等长条形工件的批量处理。其核心价值不仅在于效率提升,更在于通过 “连续、稳定、可控” 的工艺,消除了人工操作导致的质量波动,成为金属平面硬化处理中 “降本增效” 的典范方案。对于需要规模化生产的企业,这种在线化布局几乎是保证产品一致性的唯一选择。