银触点(广泛用于继电器、接触器等电气元件)的焊接质量直接影响导电性能与使用寿命,半自动化高频焊接设备通过 “人工预装 + 自动焊接” 的模式,在保证焊接精度的同时兼顾灵活性,尤其适配中小批量、多规格银触点的生产需求,以下是其工作流程与核心优势解析。
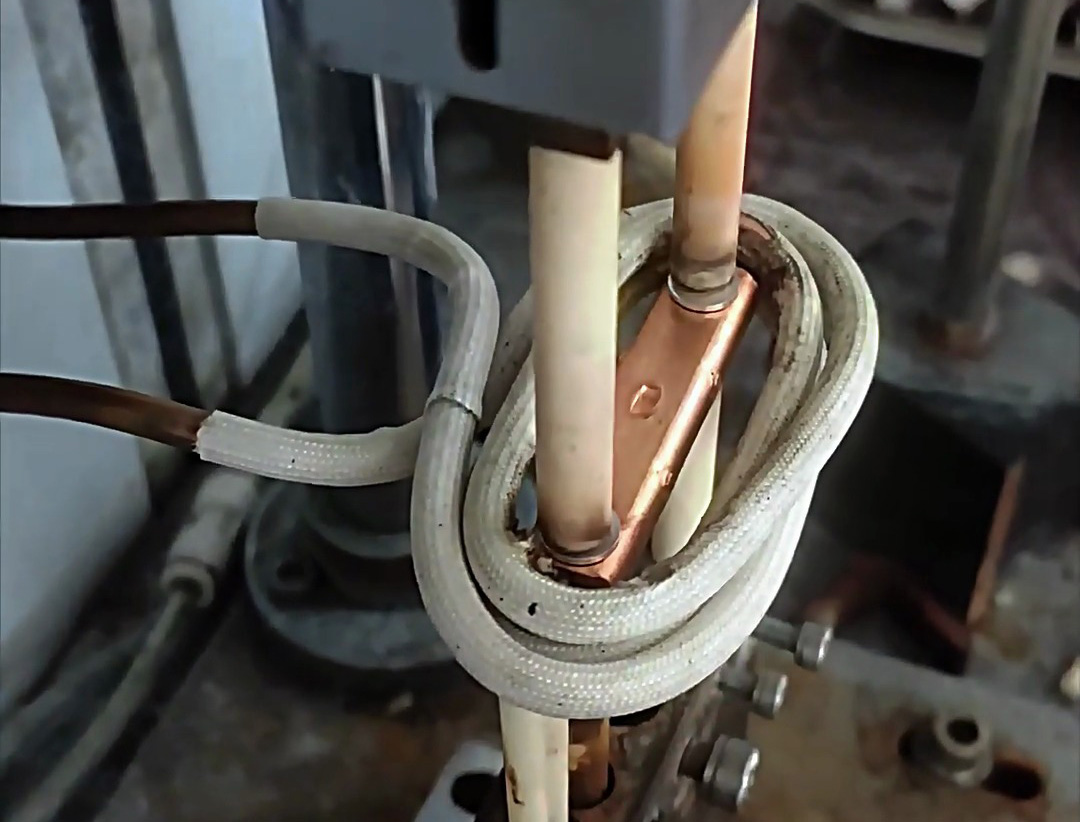
整套设备的操作环节清晰划分 “人工辅助” 与 “自动核心”,实现效率与质量的平衡:
人工前置操作(30-40 秒 / 件)
涂焊料:工人用专用工具在银触点或待焊基材(多为紫铜、黄铜)的接合面,均匀涂抹薄层焊料(常用银铜焊料,熔点 650-700℃),确保焊料覆盖整个接触区域(厚度控制在 0.1-0.2mm,避免过多溢出);
触点安装:将银触点精准放置在基材预设位置(如铜片的触点凹槽),用定位工装临时固定(防止焊接时移位);
装夹模具:工人将预装完成的工件放入高频焊机的专用模具中,模具通过机械定位确保工件与感应线圈的相对位置固定(间隙 2-3mm,保证磁场集中)。
自动焊接环节(5-10 秒 / 件)
高频加热:启动设备后,高频焊机(频率 30-60kHz)自动输出预设功率(根据银触点尺寸调整,通常 5-15kW),感应线圈产生交变磁场,使银触点与基材接触区域在 3-5 秒内快速升温至焊料熔点,焊料熔融并浸润接合面;
保压冷却:加热完成后,设备自动切换至保压状态(模具施加 5-10N 压力,确保接合紧密),同时启动风冷(或水冷),3-5 秒内完成焊料凝固;
自动停机:焊接完成后设备发出提示音,模具自动松开。
人工收尾操作(10 秒 / 件)
工人取下工件,检查焊口外观(无气泡、无虚焊),放入周转箱,进入下一循环。
相较于全人工焊接(效率低、一致性差)和全自动化生产线(投入高、换型难),这套半自动化设备的适配性显著:
质量稳定性:自动焊接阶段的功率、时间、压力参数完全固定,焊口强度波动≤5%(人工焊接可达 ±20%),银触点焊接后的导电电阻稳定在 0.01Ω 以下(符合电气元件标准);
柔性生产:更换银触点规格(如直径 3mm 换成 5mm)时,仅需更换模具与调整参数(10 分钟内完成),适合多品种、小批量订单(全自动化线换型需 1-2 小时);
成本平衡:设备投入约为全自动化线的 1/3,且对工人技能要求低(培训 1 天即可上岗),单班(8 小时)产能可达 800-1200 件,满足中小厂家的生产需求。
某电器厂的应用数据显示:采用该设备后,银触点焊接的合格率从人工焊接的 82% 提升至 98%,且因焊料用量精准(自动加热减少浪费),材料成本降低 15%。
这套半自动化设备特别适合:
中小型继电器、断路器的银触点焊接(触点直径 1-10mm);
定制化电气元件生产(规格多变,全自动化线不经济);
新产品试产阶段(快速调整工艺参数,验证焊接效果)。
为保证焊接质量,需注意:
模具精度:模具定位误差需≤0.05mm,否则会导致焊口偏移;
参数校准:每批次生产前试焊 3-5 件,通过金相检测确认焊层厚度(建议 0.05-0.1mm),再锁定参数;
线圈维护:每周清理感应线圈表面的氧化层(确保磁场强度稳定),延长线圈使用寿命(可达 1 万次以上)。
银触点半自动化高频焊接设备的本质是 “让人工做擅长的柔性操作(预装、取放),让机器做精准的重复劳动(加热、保压)”,在保证焊接质量的同时,兼顾了生产灵活性与成本控制,成为中小规模银触点焊接的 “性价比之选”。对于追求 “质量达标 + 快速响应” 的厂家而言,这种 “半自动化” 恰恰是平衡效率与投入的最优解。