铜板对焊(如变压器铜排、保险丝连接)需实现 “低电阻、高强度” 的冶金结合,高频加热机凭借 “局部快速升温 + 精准控温” 特性,成为铜板对焊的高效工具,其工艺稳定性与应用广泛性在电器制造领域尤为突出。
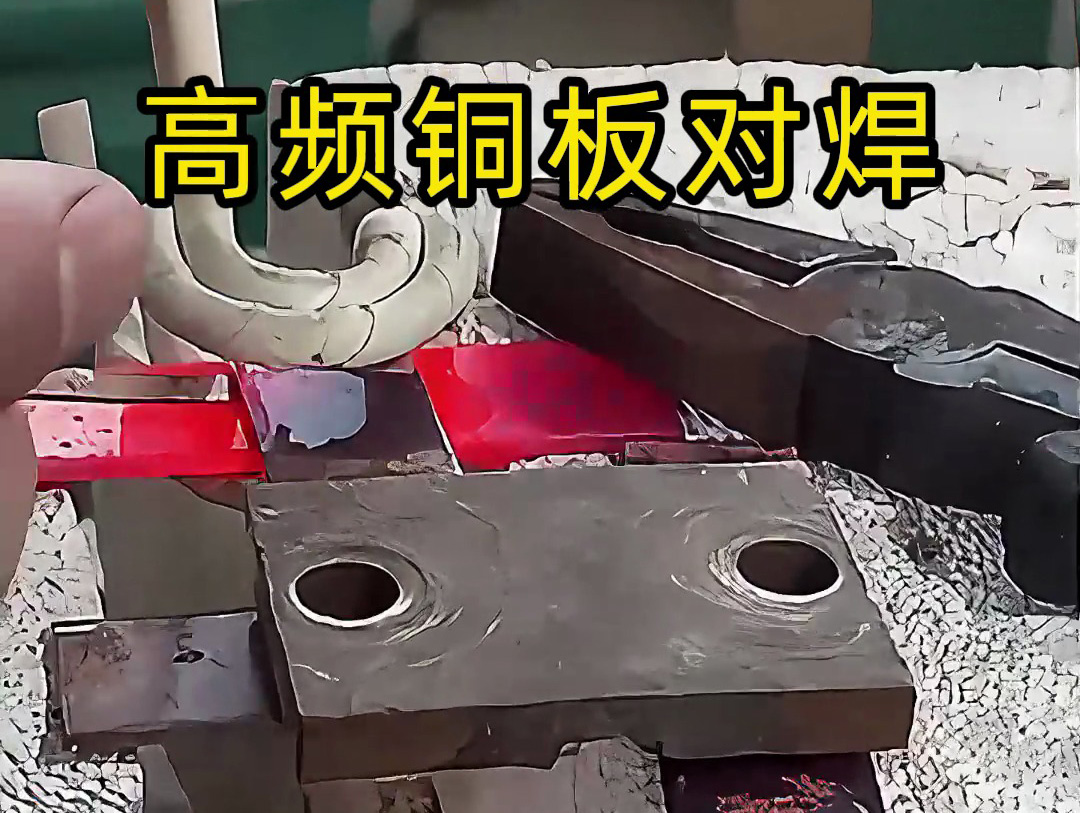
铜板(多为 T2 紫铜、TU1 无氧铜)导电性强、导热快,传统焊接(气焊、电弧焊)易因加热慢、热影响区大导致:
接头氧化(生成 CuO,电阻增大);
铜板变形(影响装配精度);
结合强度低(冷态剪切强度≤150MPa)。
高频加热对焊通过以下方式突破瓶颈:
高频感应线圈(频率 30-60kHz)紧贴铜板对接缝,利用铜的涡流发热特性,使接缝区域在 1-3 秒内快速升温至 1083℃(铜的熔点),而接缝外 5mm 区域温度≤100℃,完全避免铜板因整体受热导致的氧化变色(表面仍保持紫铜本色)和翘曲变形(平面度误差≤0.02mm/m)。
加热至熔融状态时,通过气动夹具施加轴向压力(0.5-2MPa),使两侧铜板熔池融合并挤出氧化渣,冷却后形成致密的对接接头:
单道对接焊缝(如 100×10mm 铜排)的加热 + 加压时间仅需 3-5 秒,每小时可完成 800-1000 个接头,较气焊(每接头 30-60 秒)效率提升 10 倍以上,且无需后续打磨(熔渣已被挤出),大幅缩短工序时间。
高频加热铜板对焊的 “低电阻、高强度” 特性,使其成为以下领域的首选工艺:
变压器铜排连接:大型变压器的导电铜排(截面 50×5mm 至 200×20mm)需通过对接延伸,高频对焊确保接头电阻极小(减少输电损耗),且因变形小,可直接装配(无需校直),某变压器厂数据显示,采用该工艺后铜排装配效率提升 40%。
保险丝熔体焊接:保险丝中的铜质熔体(薄至 0.1mm)需与电极对接,高频加热的局部升温可避免熔体过热熔断,同时保证接头导电均匀(熔断电流稳定),合格率从传统焊接的 90% 提升至 99.5%。
电器端子与铜板连接:如配电柜中的铜端子与汇流排对接,高频对焊可实现 “无焊料连接”(避免焊锡影响导电性),接头耐温达 300℃以上(满足过载工况)。
对接间隙:铜板端面需平整(粗糙度 Ra1.6),对接间隙控制在 0.1-0.3mm(过大易产生未熔合,过小易挤出过量熔料);
功率匹配:根据铜板厚度调整高频功率(如 10mm 厚铜板需 15-20kW,0.1mm 薄板需 3-5kW),避免功率过高导致烧穿或过低导致未熔;
加压时机:在铜板表面出现 “镜面熔融”(约 1083℃)时立即加压,过早易产生冷焊,过晚则熔料过多导致接头凹陷。
高频加热机在铜板对焊中的应用,本质是通过 “精准的局部能量输入” 解决了铜材焊接的 “氧化、变形、效率低” 三大痛点。无论是电力传输中的大截面铜排,还是精密电器中的细小铜件,这种工艺都能以 “高强度 + 高导电 + 高效率” 的组合优势,成为铜板连接的理想解决方案,也印证了高频加热技术在金属连接领域的广泛适配性与不可替代性。