车刀作为金属切削的核心工具,其刀片(硬质合金)与刀体(高速钢 / 工具钢)的连接强度直接影响切削精度与使用寿命。高频感应加热焊接凭借 “局部快速升温、参数精准可控” 的特性,成为车刀制造中实现两者牢固结合的主流技术,完美解决了传统焊接(如气焊)的效率低、质量波动大等问题。
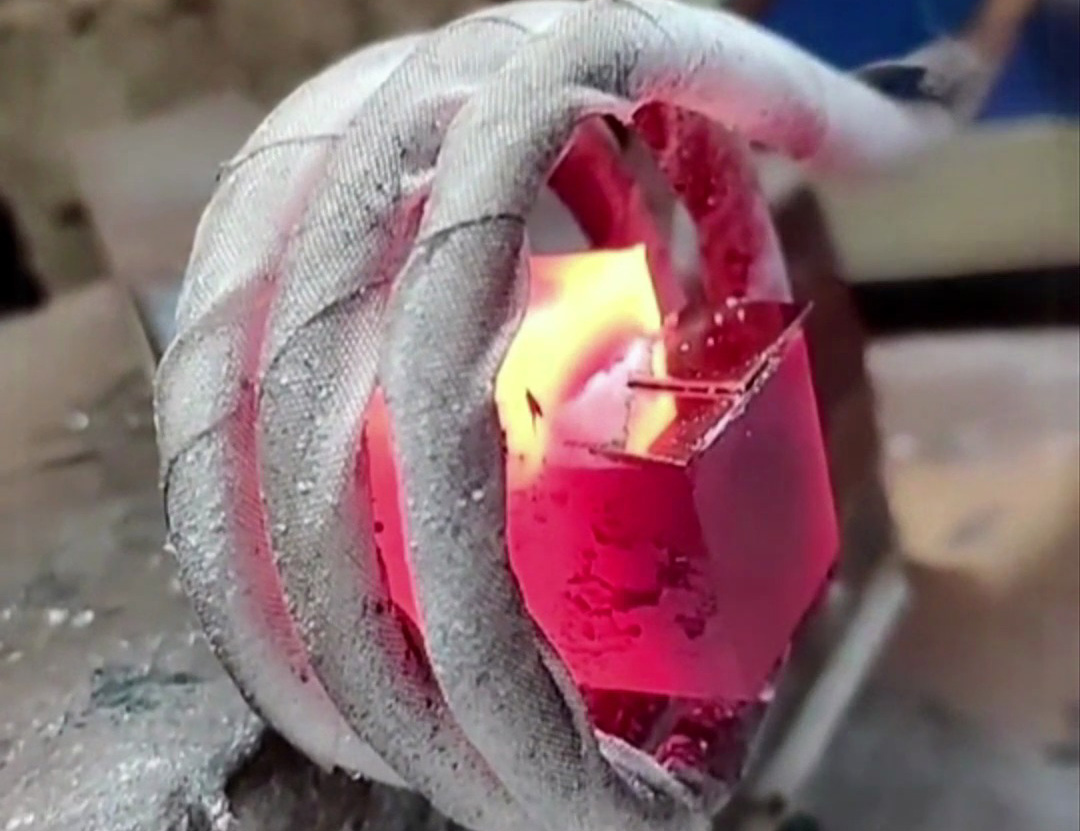
高频焊接(频率 10-50kHz)通过电磁感应实现 “定向加热”,其过程可分为三个关键阶段:
感应加热聚焦焊缝
将硬质合金刀片与刀体的接合面(通常预留 0.1-0.2mm 间隙,放置银铜焊片或焊膏)对准高频感应线圈,高频电流产生的交变磁场使接合面区域快速感应出涡流,在 2-5 秒内升温至 750-850℃(银铜焊料的熔点范围),此时焊料熔融并浸润刀片与刀体的表面。
焊料扩散形成冶金结合
熔融的焊料在毛细作用下填充接合间隙,与硬质合金(含钨、钴)和刀体钢(含铁、碳)发生微量扩散,冷却后形成牢固的冶金结合(剪切强度≥200MPa),远高于机械连接的强度。
精准控温保护材料性能
仅加热接合面及周边 1-2mm 区域,刀片和刀体的整体温度≤300℃,避免硬质合金因高温(超过 900℃)导致的脆性增加(抗弯强度下降),也防止刀体钢过热导致的晶粒粗大(韧性降低)。
车刀制造中,高频焊接较气焊、电阻焊等传统方式的提升体现在多维度:
对比项 | 高频感应焊接 | 氧乙炔气焊 |
---|
加热精度 | 局部加热,焊缝外温度≤300℃,无热损伤 | 火焰加热范围大,刀片易过热脆化 |
焊接效率 | 单件焊接时间 2-5 秒,每小时可焊 1000 + 件 | 单件需 30-60 秒,效率仅为高频的 1/10 |
结合强度 | 焊层均匀,强度波动≤5% | 火焰不稳导致焊料偏聚,强度波动 ±15% |
材料保护 | 无氧化(加热时间短),刀片性能无损 | 高温氧化导致刀片表面形成脆性层 |
某刀具厂数据显示:高频焊接的车刀,在切削 45# 钢时的使用寿命是气焊车刀的 1.5 倍,且因焊层均匀,切削过程中刀片脱落率从 0.5% 降至 0.01%。
车刀高频焊接的质量依赖严格的参数控制:
线圈设计:采用 “C 型” 或 “环形” 专用线圈,确保磁场集中于接合面(偏离量≤0.1mm),避免刀片或刀体局部过热;
功率与时间:根据刀片尺寸(如 10×10mm 硬质合金刀片)调整功率(3-8kW),加热时间误差≤0.1 秒(防止焊料过烧或未熔);
焊前清理:接合面需经喷砂或酸洗处理(粗糙度 Ra1.6-3.2μm),去除氧化层和油污,确保焊料浸润充分;
冷却控制:焊接完成后自然冷却(避免急冷导致应力裂纹),焊后可进行 200-250℃低温回火,消除残余应力。
高频焊接技术为车刀性能提升提供了三大支撑:
保障切削可靠性:高结合强度确保车刀在高速切削(转速 3000r/min 以上)和重载(切削力≥500N)下不出现刀片脱落;
延长使用寿命:精准控温避免刀片性能损伤,车刀的抗冲击性和耐磨性显著提升,平均寿命延长 50% 以上;
适配复杂刀具结构:可焊接异形刀片(如菱形、三角形)和细长刀体,满足精密车削(如数控车床)对刀具精度的要求(刃口跳动≤0.01mm)。
高频感应焊接通过对 “热输入” 的极致控制,完美解决了车刀制造中 “硬质合金与钢的异种材料连接” 难题,其高效性与质量稳定性使其成为现代刀具工业的核心工艺。对于追求 “高精度、长寿命” 的车刀产品,高频焊接不仅是生产效率的保障,更是性能突破的关键 —— 毕竟,一把焊接牢固、性能稳定的车刀,才能在金属切削中 “所向披靡”。