在要求较低的电机转子热装配场景(如小型农用电机、简易机械设备)中,仅用一台高频加热设备、依赖经验控制的简易工艺,虽缺乏测温控温系统,却能以低成本满足基础装配需求,其核心逻辑是 “经验替代精度”,适配对装配间隙、结合强度要求不极致的场合。
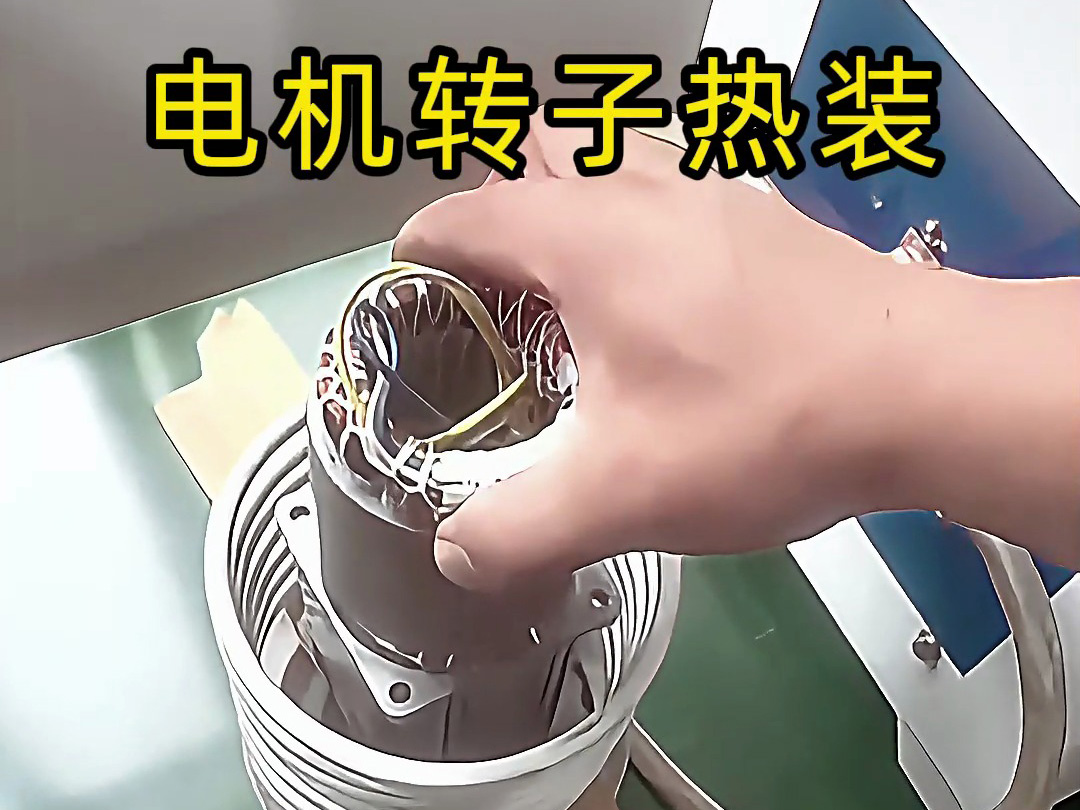
这种简易工艺省去了红外测温、PLC 控温等精密组件,全流程依赖操作工经验,核心步骤如下:
加热时长的经验判断
根据电机铝壳尺寸(如直径 100mm、高度 80mm 的 ADC12 铝壳),操作工通过 “手感温度” 或 “加热时长” 控制:
装配时机的经验把控
加热完成后,操作工需在 30 秒内完成转子插入:
最终结合的基础保障
装配后铝壳自然冷却收缩,与转子形成过盈配合(结合强度约 100-150MPa),虽不及精密控温工艺(200-300MPa),但足以满足低转速(≤1500r/min)、轻负载(功率≤1.5kW)电机的运行需求,不会出现转子打滑。
这种简易工艺的生存空间,在于适配 “低要求、低成本” 的生产需求:
小型农用电机:如水泵电机、风机电机,对转子与铝壳的同心度要求低(允许 ±0.1mm 偏差),运行时振动、噪音要求不严格;
维修翻新场景:电机维修时临时装配,无需长期稳定性,快速完成热装即可投入使用;
低成本批量生产:如玩具电机、小型传动电机,单价低(≤50 元),无需投入精密设备,依赖熟练工经验可将合格率控制在 85% 以上。
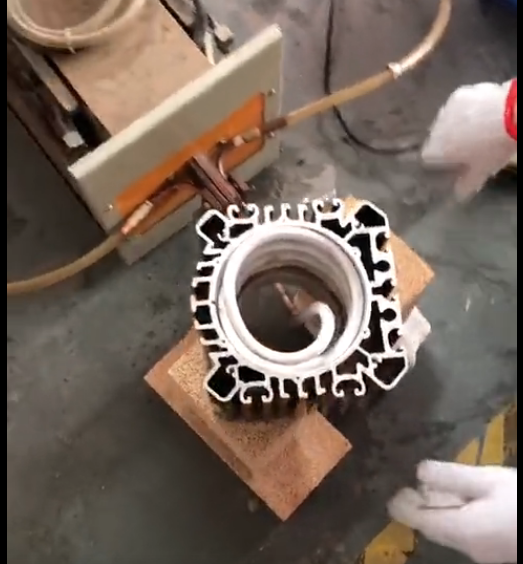
这种工艺的短板也十分明显,决定了其无法用于高要求场合:
质量稳定性差:同一批铝壳加热时间相同,因壁厚不均、初始温度差异,可能出现部分加热过度、部分不足,合格率波动 ±10%;
铝壳易损伤:无控温易导致局部过热(超过 200℃),使铝壳出现微裂纹或变形,影响电机寿命(运行 1000 小时后故障率较高);
效率受限:熟练工每小时最多装配 30-40 台,远低于带控温系统的自动化生产线(100 + 台 / 小时)。
这种仅靠高频加热设备和经验控制的电机铝壳热装工艺,是 “低成本优先” 理念下的务实选择 —— 虽无精密控温的稳定性,却能以最低投入满足基础装配需求,在对电机性能要求不高的场景中仍有其存在价值。但其本质是 “经验替代技术”,无法替代带测温控温的标准化工艺,这也决定了它只能作为特定场景的补充方案。