实心棒料(如碳钢、合金钢棒)在热锻、热弯、调质等工艺中需快速均匀升温,高频感应加热机凭借 “电磁感应直接生热” 的特性,突破传统加热(燃煤、燃气炉)的效率与均匀性瓶颈,成为棒料热加工的优选方案,尤其在批量生产中能显著提升工艺稳定性与经济性。
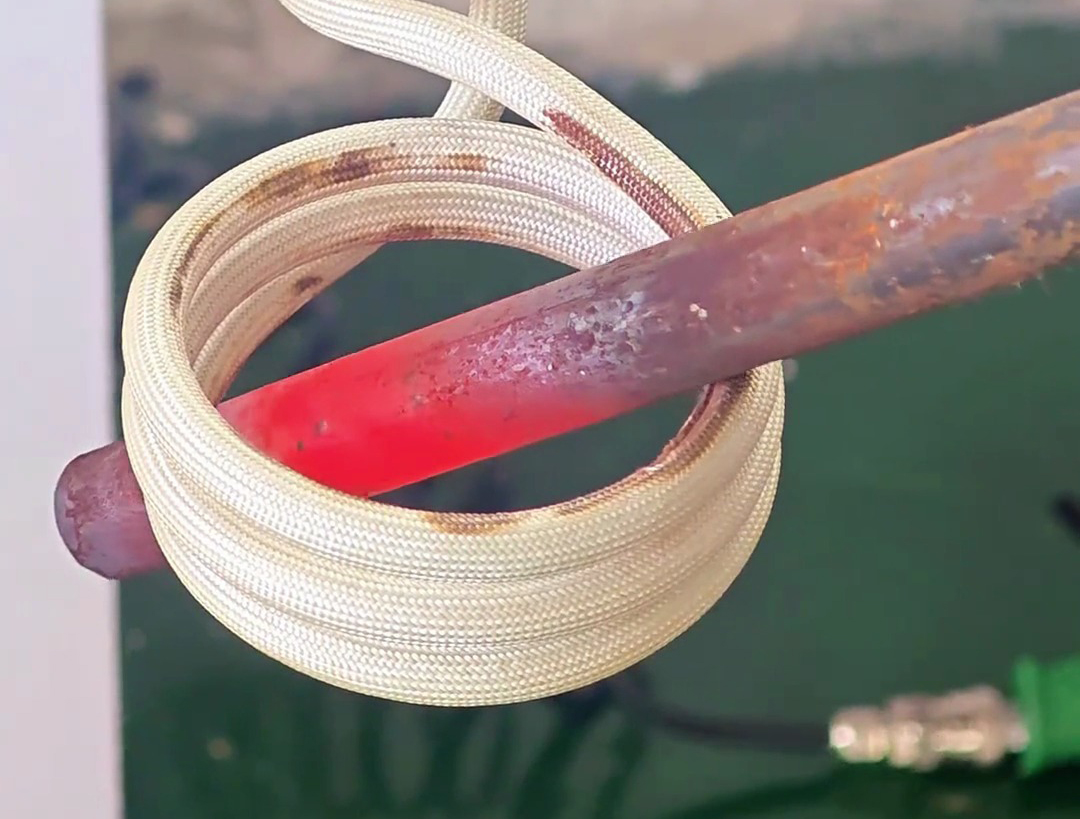
高频感应加热(频率 10-500kHz)通过交变磁场在棒料内部诱导涡流产生热量,从根本上改变了热量传递方式,其优势体现在:
高频电流的趋肤效应使热量集中在棒料表层(深度 0.5-3mm),并快速向芯部传导。以直径 50mm 的 45# 钢棒为例:
高频感应线圈环绕棒料布置,磁场均匀覆盖圆周,配合棒料旋转(5-15r/min),可使:
通过 PLC 系统可精准设定加热参数,满足多样化工艺:
热锻前加热:设定温度 1050-1150℃,确保棒料塑性最佳(延伸率≥30%),锻造后晶粒细化均匀;
调质前加热:设定温度 850-900℃,配合后续淬火 + 回火,使棒料整体硬度偏差≤±1HRC;
局部退火:通过线圈局部聚焦,仅加热棒料特定区域(如端部 100mm)至 600-700℃,消除冷加工应力,保留其他区域强度。
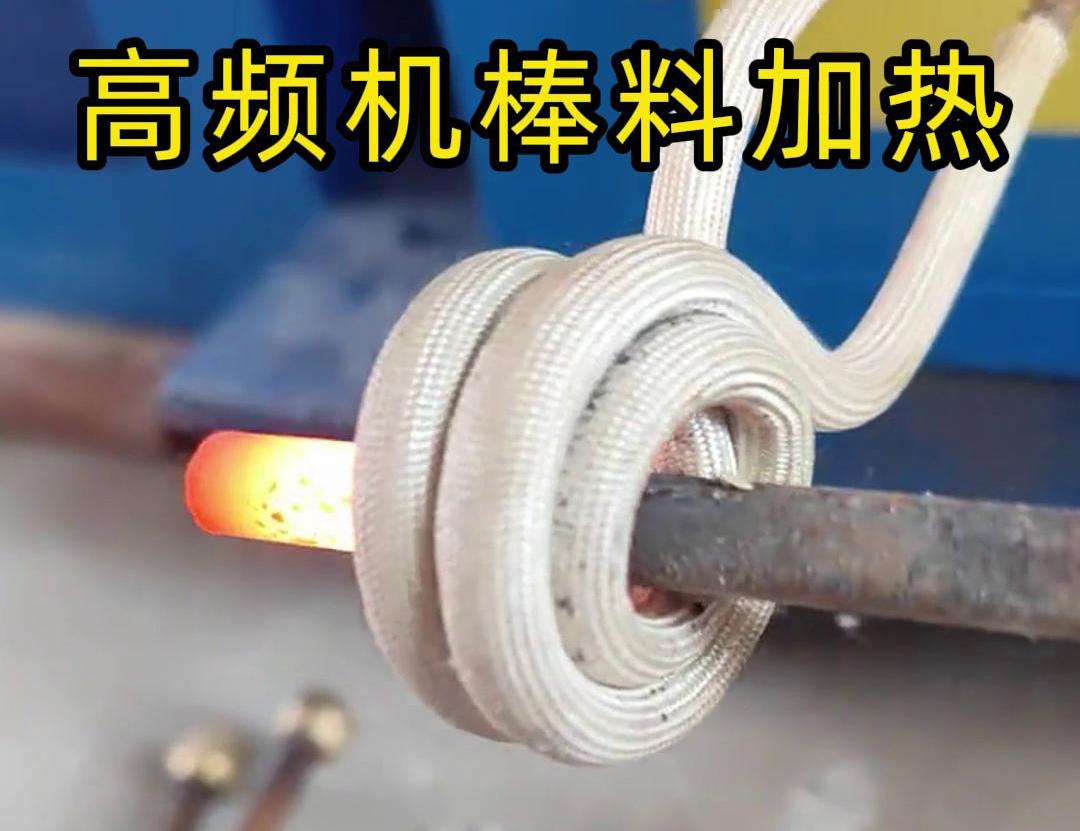
高频感应加热机对实心棒料的适配性广泛,从细棒到中粗棒均能高效处理:
棒料直径(mm) | 高频频率(kHz) | 典型工艺场景 | 单根加热时间(分钟) |
---|
10-30 | 100-500 | 小件热锻(如螺栓坯、销轴) | 1-3 |
30-80 | 30-100 | 中型棒料热弯、调质(如传动轴) | 5-15 |
80-150 | 10-30 | 大型棒料热锻前预热(如齿轮坯) | 15-30 |
汽车半轴棒料热锻:直径 60mm 的 40Cr 棒料,高频加热至 1100℃(8 分钟),热锻后毛坯精度提升(直径误差≤±0.5mm),氧化皮重量减少 35%,后续机加工时间缩短 20%;
工程机械销轴调质:直径 80mm 的 45# 钢棒,高频加热至 860℃(12 分钟),淬火后硬度均匀(HRC50-52),较传统炉淬(硬度差 5HRC)合格率提升至 99%;
五金工具杆部局部退火:直径 20mm 的扳手杆,高频线圈聚焦加热端部 50mm 区域至 650℃(2 分钟),退火后端部硬度从 HRC35 降至 HRC20,便于后续铆接手柄,非退火区仍保持原强度。
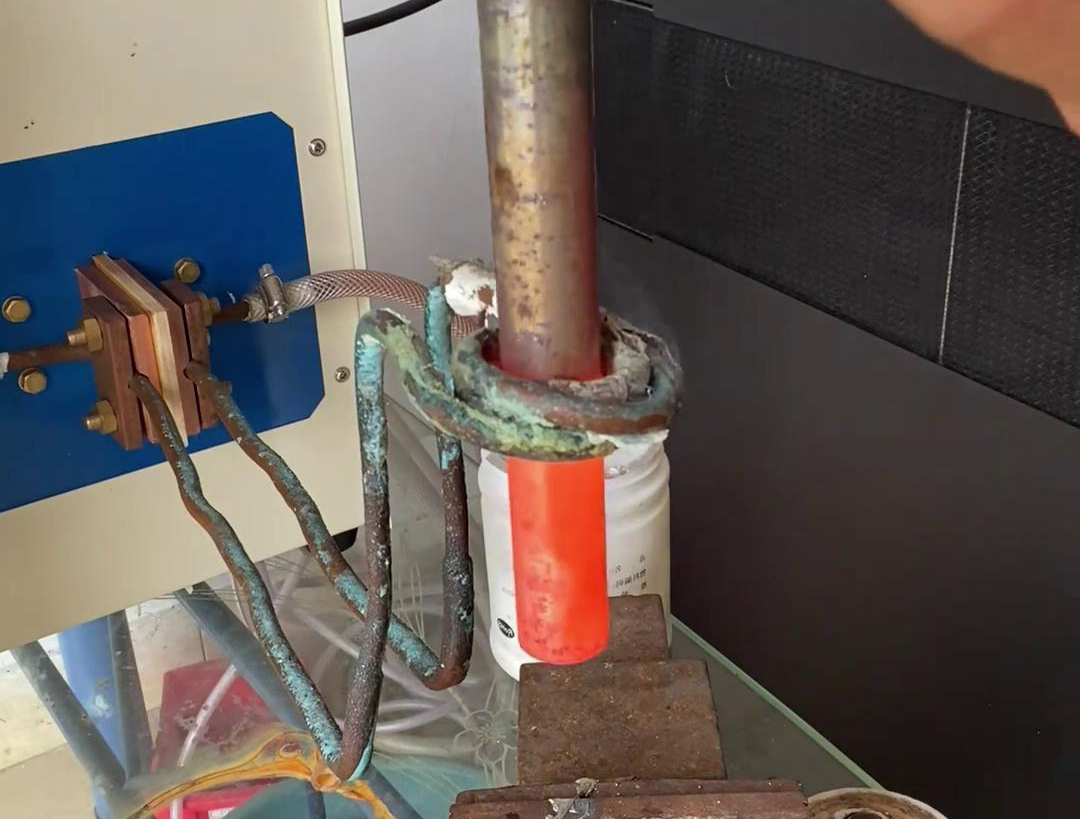
对比项 | 高频感应加热机 | 燃煤 / 燃气炉 | 电阻炉 |
---|
加热效率 | 热效率 60%-70%,升温速度快 | 热效率≤30%,升温慢 | 热效率 50%-60%,但加热均匀性差 |
环境友好 | 电加热无废气,噪音≤60dB | 排放烟尘、CO,污染严重 | 用电但升温慢,能耗较高 |
自动化适配 | 可配合送料机实现连续生产 | 需人工上料翻料,自动化困难 | 批量式加热,难连续生产 |
质量稳定性 | 温度偏差≤±5℃,合格率≥98% | 偏差≥30℃,合格率≤85% | 偏差 ±15℃,合格率≤90% |
高频感应加热机对实心棒料的处理,本质是通过 “能量直接作用于工件” 实现 “高效、均匀、可控” 的加热效果。无论是批量热锻的快速升温,还是精密调质的精准控温,其性能都远超传统加热方式,成为现代棒料热加工中 “提质、降本、增效” 的核心设备,尤其适配自动化生产线的节拍需求,推动热处理工艺向 “绿色化、智能化” 升级。