据统计,国内铝合金熔铸的综合能耗高于国外约8%~10%,产品的综合成品率却低约10%。因此,提高铝合金熔炼过程的热效率,提高铸件质量和成品率,节约资源能耗,已显得十分迫切,这也是企业降本增效,增强企业竞争力的重要手段。因此,寻找铝合金熔炼炉的节能方法和措施,提高熔炼炉的热效率显得至关重要。 铝合金熔炼炉的熔炼过程大致可分为4个阶段,即炉料装入—软化下榻—炉料化平—全部熔化。对铝料的加热是通过烧嘴火焰的对流传热、火焰和炉墻的辐射传热以及铝料间的传导热来完成的,整个过程中,三者之间比率不断变化,固态时铝的黑度小,导热能力强,随着熔炼的进行,炉料进入半固态,导热能力下降,热力学性质发生了根本的变化,液态铝的导热能力仅为固态铝的40%,熔池上部向底部的传导传热过程十分缓慢。
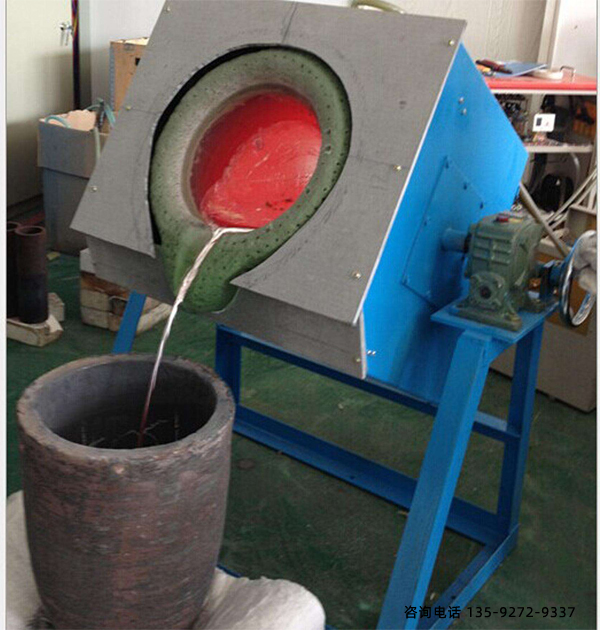
熔铝炉能平衡图 1 烟气带走热量节能分析及措施 对于火焰反射炉来讲,在铝的熔化期,炉内温度一般控制在1100℃-1200℃,此时的出炉烟气温度即为炉内气氛温度,经计算,烟气带走的热量约占炉子热负荷的60%左右,如果不充分利用这部分余热,将造成巨大的热能损失,同时给环境带来热污染和烟气污染。 因此,应充分利用热传导和烟气余热,减少排放烟气带走的热量,实现熔铝炉的节能,具体措施可采取: 1. 采用高速均匀化烧嘴,对炉料进行喷射加热,改善炉内空气循环,强化炉内传热。高速喷嘴使燃气获得充分燃烧,提高了燃烧值,减少了燃料的损失,提高了热效率。 2. 采用蓄热式高温烟气燃烧技术和余热梯级利用技术,充分利用烟气余热,提高风温,减少热量损失。目前,蓄热式熔铝炉已经得到一定规模应用,研究表明,采用蓄热式熔铝炉可节能60%,极大提高熔铝炉的热效率,余热梯级技术利用可使烟气排放温度达到150℃左右,减少了热损失。 2 过量空气系数控制节能分析及措施 在燃料流量一定的情况下,过量空气系数过大,将导致大量空气未参与燃烧就进入炉膛,这些空气将降低炉温,随烟气携带走大量的热量,导致熔铝炉能耗较高。经计算,在650℃排烟温度条件下,当过量空气系数等于1时,即没有大量未参与燃烧空气情况下,排气热损失在30%左右,而在同等排烟温度时,如果过量空气系数为1.5时,则排气热损失达到41%。 由此可见,控制过量空气系数对提高热效率具有重大意义。当然,过量空气系数也不能小于1,否则会造成燃料不完全燃烧,燃料的化学热不能充分释放出来,而损失大量能量。同时,由于燃料的不完全燃烧,还会产生有毒有害气体,污染环境。 在实际生产中,烧嘴燃料量不是一成不变的,这就要求助燃空气量要随着燃料量的波动而调整,否则,将导致排烟中含有可燃气体或排烟中含有大量空气,影响熔铝炉的节能效果,甚至带来安全隐患。所以为实现过量空气系数可控,可采取以下措施: 1. 精确测定燃料流量流速,实现流量流速的快速精确控制,保持燃料流速的稳定。 2. 安装烟气分析仪和反馈装置,测量烟气成分,并将信息即时反馈给主机,进行助燃空气流量控制,使过量空气系数为1-1.05,确保熔铝炉处于最佳燃烧工作状态。 3. 改善烧嘴处燃料喷出状态,使燃料成雾化分散喷出,从而助燃空气量理论值和实际值更接近。
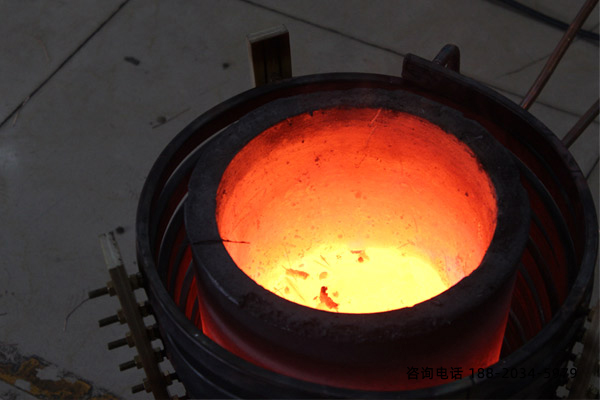
熔铝炉节能系统现场照片 3 炉壁炉门节能分析及措施 在熔铝炉的热损失途径中,炉壁炉门散热损失是仅次于排烟烟气的热损失,熔炼过程热损失的15%-25%,特别是出料口、炉门等处的漏热非常大。尽管高温铝液本身的发射率较低,但是铝液上面漂浮的一层氧化物发射率较高,况且辐射换热与热力学温度的四次方成正比,因此,炉壁炉门热损失特别大,另外,个别耐火材料和保温介质破损地方往往引起局部漏热,导致炉内热量散失。 因此,为减少炉料炉门的热损失,提高热效率,可采取如下措施: 1. 在炉门和取料口处采用优化设计的反射罩结构,起到遮热板的作用,防止热量的大量散失。 2. 采用封闭式电磁搅拌技术进行熔液的温度均匀化和成分均匀化,减少熔炼过程中炉门开启时间,减少热损失。 3. 采用短流程熔铸工艺,流槽内铺垫保温介质,减少取料口和输送过程中铝液热损失。 4. 定期检查炉壁,避免炉壁局部破损,引起漏热,或者安装热成像仪,对炉壁温度进行监控,及时修补引起漏热的炉壁。 5. 炉壁炉门采用绝热或隔热性能好的材料。 4 炉温均匀性节能分析及措施 在大型熔铝炉中,炉温分布不均匀会导致铝液烧损,烟气中氧化铝含量增加,烟气排放温度升高,同时炉膛内高温区可能使炉壁温度超限,缩短熔炼炉寿命。由于炉内温度不均,亦造成炉壁炉门热损失增大,消耗更多能量。为减少炉温不均造成的影响,可采取如下措施: 1. 合理设计烧嘴喷射的角度,防止出现升温死角。一般情况下,圆形熔铝炉内气氛流动较均匀,不易出现升温死角,方形熔铝炉由于结构的限制,在四角处容易出现升温死角,因此,应合理设计烧嘴喷射角度,增加炉内气氛流动性,分散受热面积,使炉内温度场均匀化。 2. 铝熔化平后进行适当电磁搅拌,让铝液在炉内实现紊流,进行热对流,实现铝液温度的均匀化和成分均匀化,减少局部过热。 5 炉渣节能分析及措施 作为铝合金熔炼时的杂质,炉渣是必须与铝液分离的,生成炉渣的因素很多(包括氧化烧损、炉内杂质等),因炉渣带造成的热损失约占铝熔炉热损失5%左右,这些热损失主要由炉渣带走的热和扒渣时散失热组成,因此,为减少这部分热损失,可采取以下措施: 1. 减少炉渣的生成量,通过减少氧化烧损,采用纯净原材料,降低炉门打开频次,改善炉内气氛等措施减少炉渣生产量。 2. 减少扒渣时间,减少热损失。通过合理设计抄灰房位置,使用专用扒渣工具来减少扒渣时间。
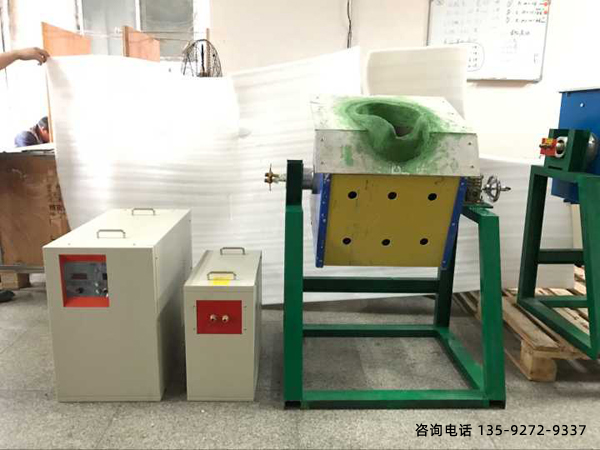
某铝企熔铝炉余热利用设备 根据以上分析,通过采用陶瓷球式蓄热式系统、电磁搅拌短流程熔铸工艺、高速均匀化烧嘴、反射罩式炉门、定期检查炉膛、使用专用扒渣工具等装置或措施,使铝合金熔炼炉节能约65%,排烟温度降低到500℃左右,有效地减少了热量损失和污染物排放,降低了生产成本。
东莞铝合金熔炼炉生产厂家-提高炉子寿命 深圳铝合金熔炼炉内冶铝合金反映的基本定律 铝合金熔炼炉-如何提高热效率、降低其能耗 铝合金熔炼炉-电磁感应搅拌器 铝合金熔炼炉-可保持自动式没有人实际操作